High-Performance
Modular Battery Solutions
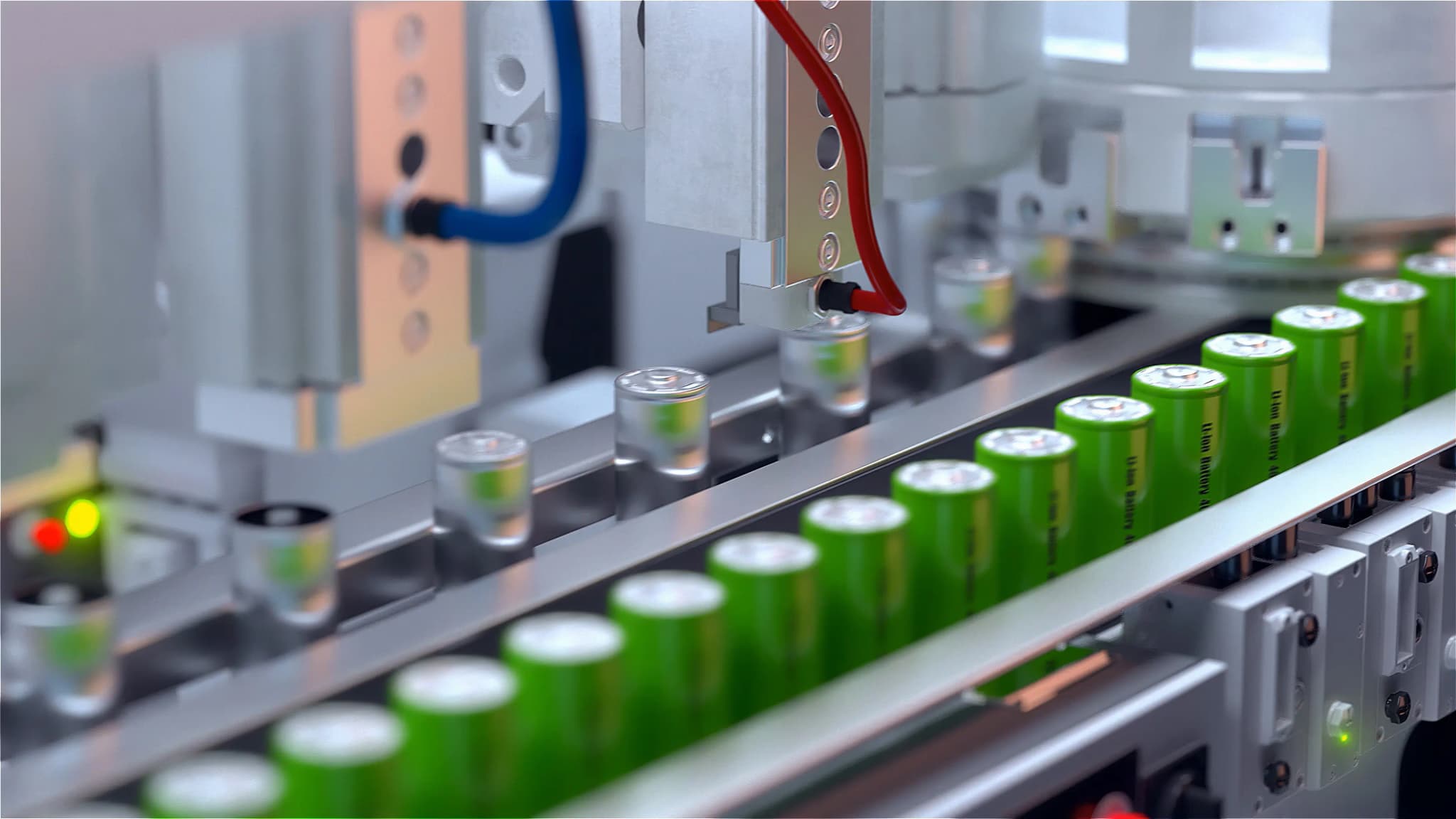
Explore our range of high-performance battery modules, each designed to deliver exceptional energy density, built-in safety, and certified quality for versatile applications.
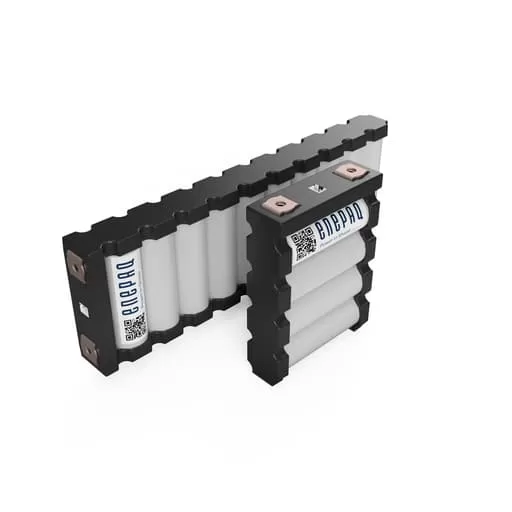
Molicel P42A 21700 Li-ion Battery Module
Battery module from 1s1p to 1s10p with 21700 size cells.
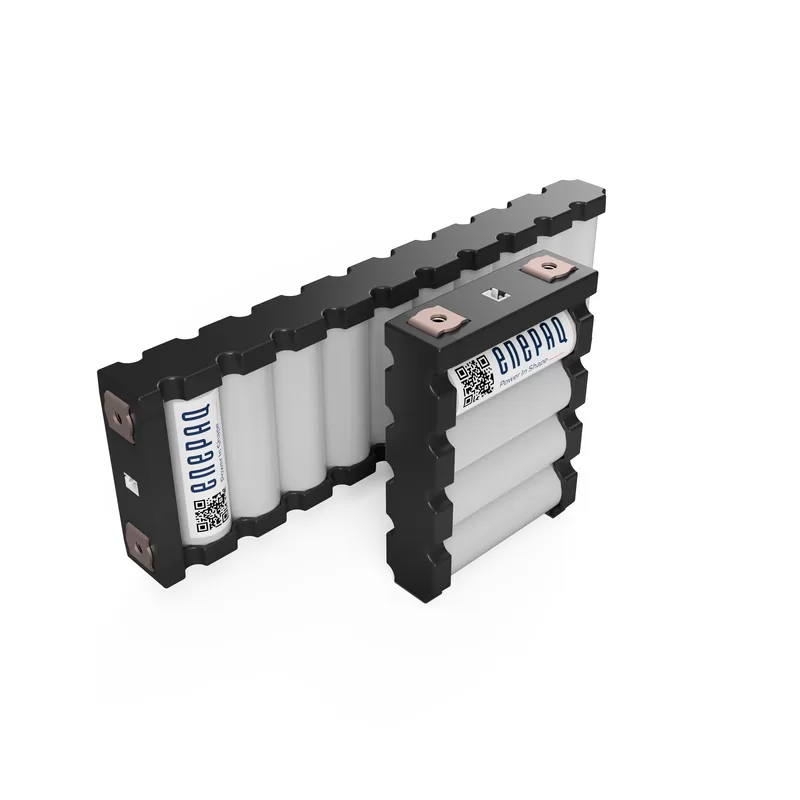
Molicel P45B 21700 Li-ion Battery Module
Battery module from 1s1p to 1s10p with 21700 size cells.
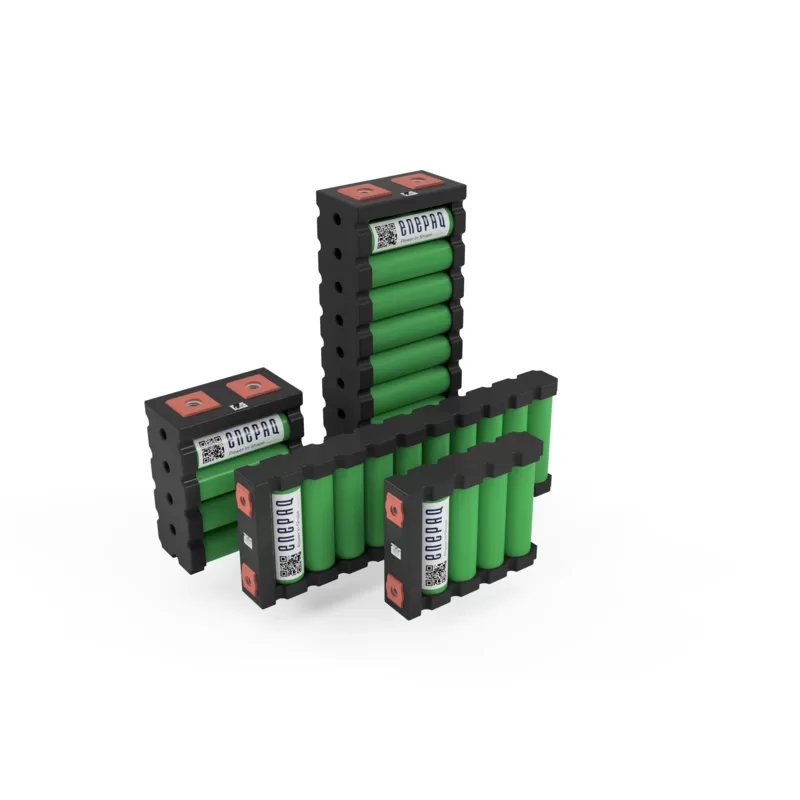
VTC6 Sony/Murata 18650 Li-ion Battery Module
Battery module from 1s1p to 1s20p with 18650 size cells.
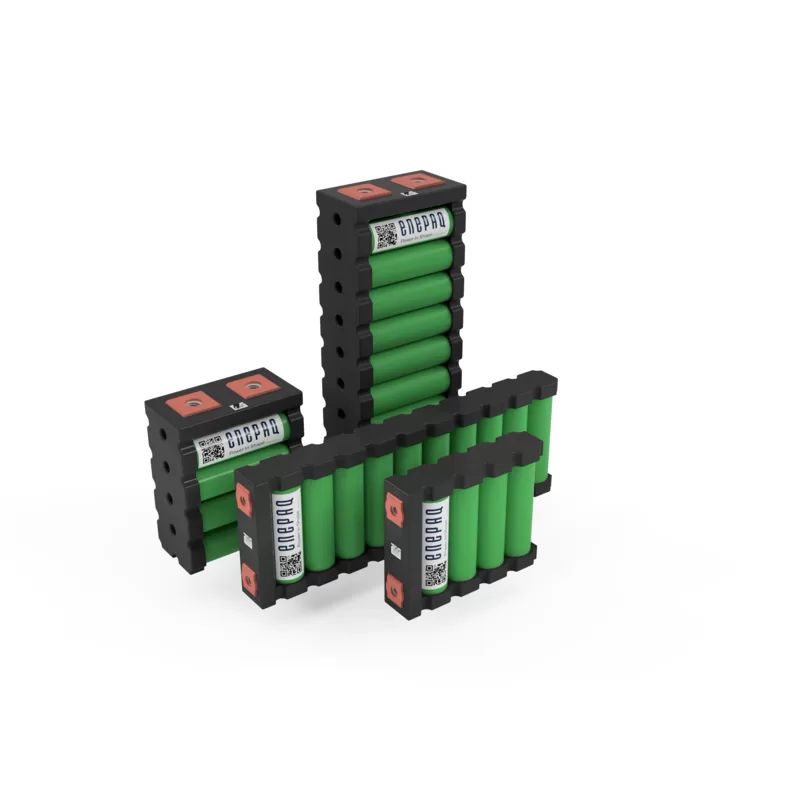
VTC5A Sony/Murata Li-ion Battery Module
Battery module from 1s1p to 1s10p with 18650 size cells.
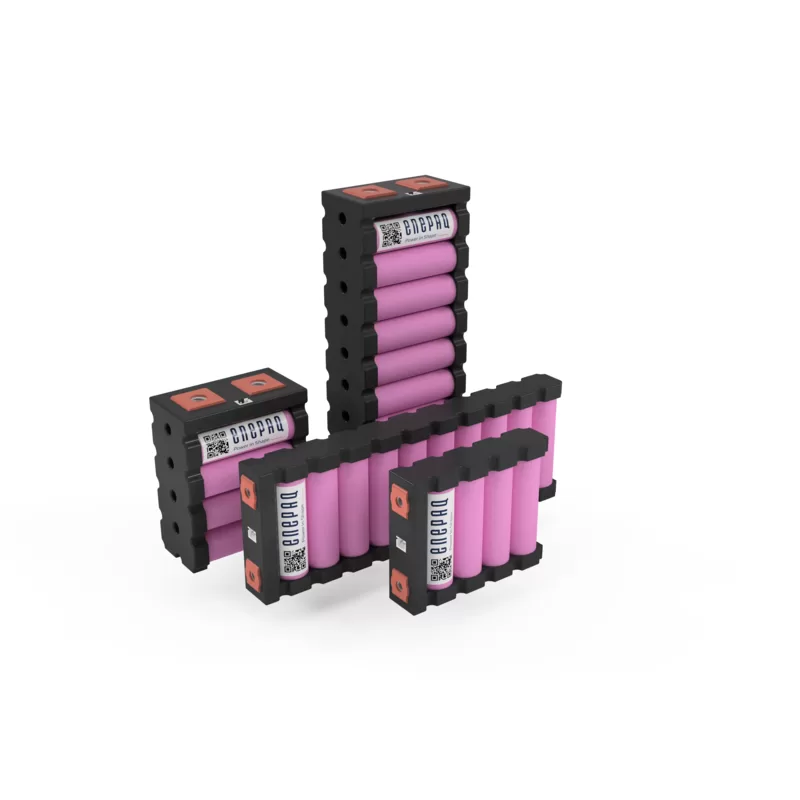
Samsung 30Q 18650 Li-ion Battery Module
Battery module from 1s1p to 1s20p with 18650 size cells.
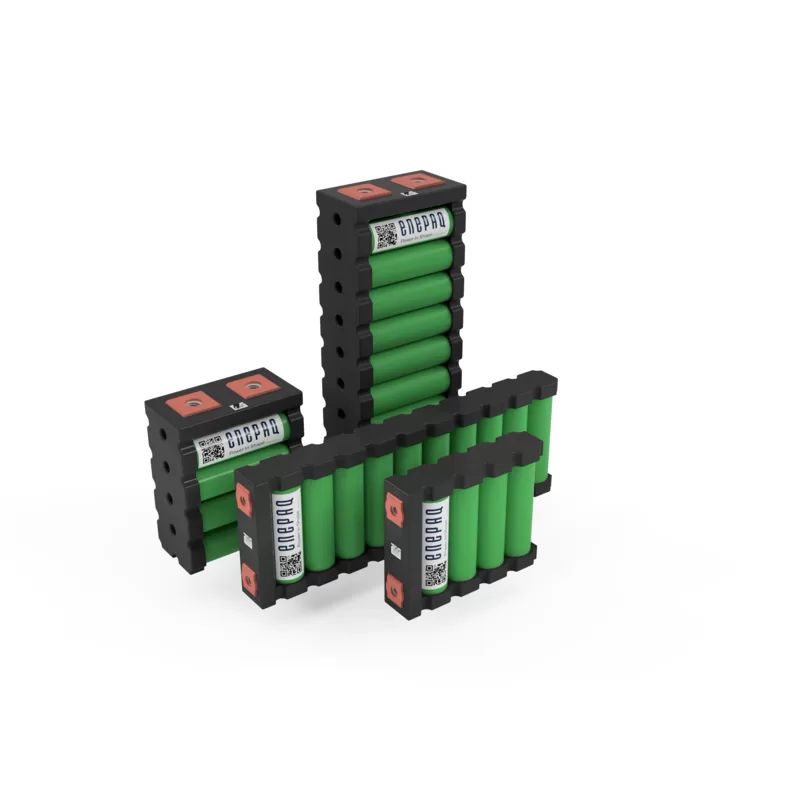
Samsung 25R 18650 Li-ion Battery Module
Battery module from 1s1p to 1s20p with 18650 size cells.
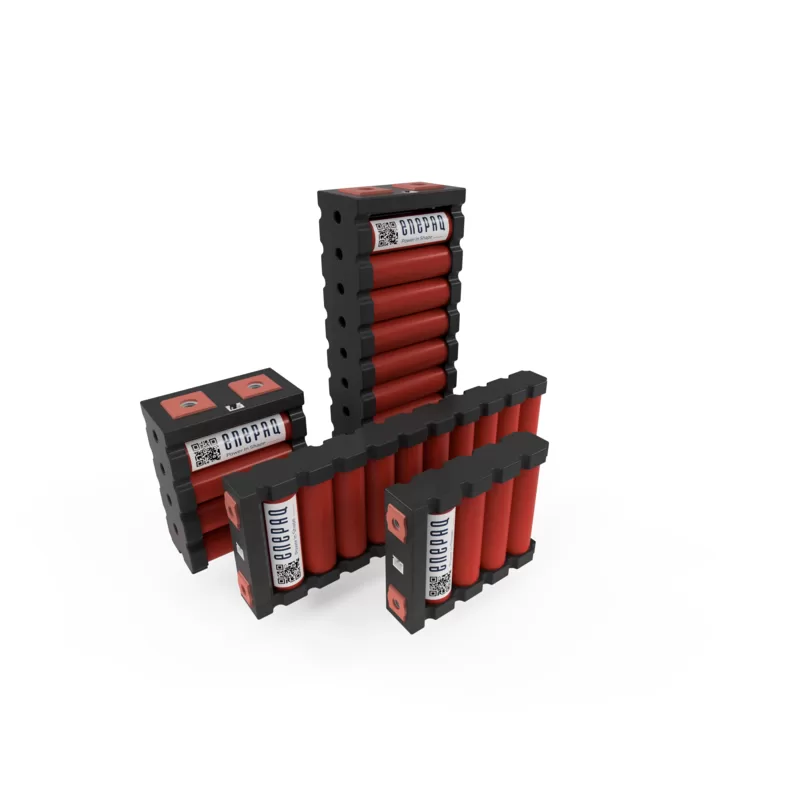
Sanyo GA 18650 Li-ion Battery Module
Battery module from 1s1p to 1s20p with 18650 size cells.
Efficient, Safe, and Scalable Energy Solutions
Our battery modules are engineered to combine high energy density with advanced safety features, offering reliable performance across a wide range of applications. With their lightweight, compact design, they maximize power output while minimizing space requirements, making them ideal for projects where efficiency and portability are critical.
Built to meet the highest international standards, our modules are certified for safety and durability, ensuring long-lasting operation even in demanding environments. From electric vehicles to renewable energy systems, our modular solutions provide the flexibility and scalability you need to power innovation.
Key Features and Benefits
Application
Powering Innovation Across Industries
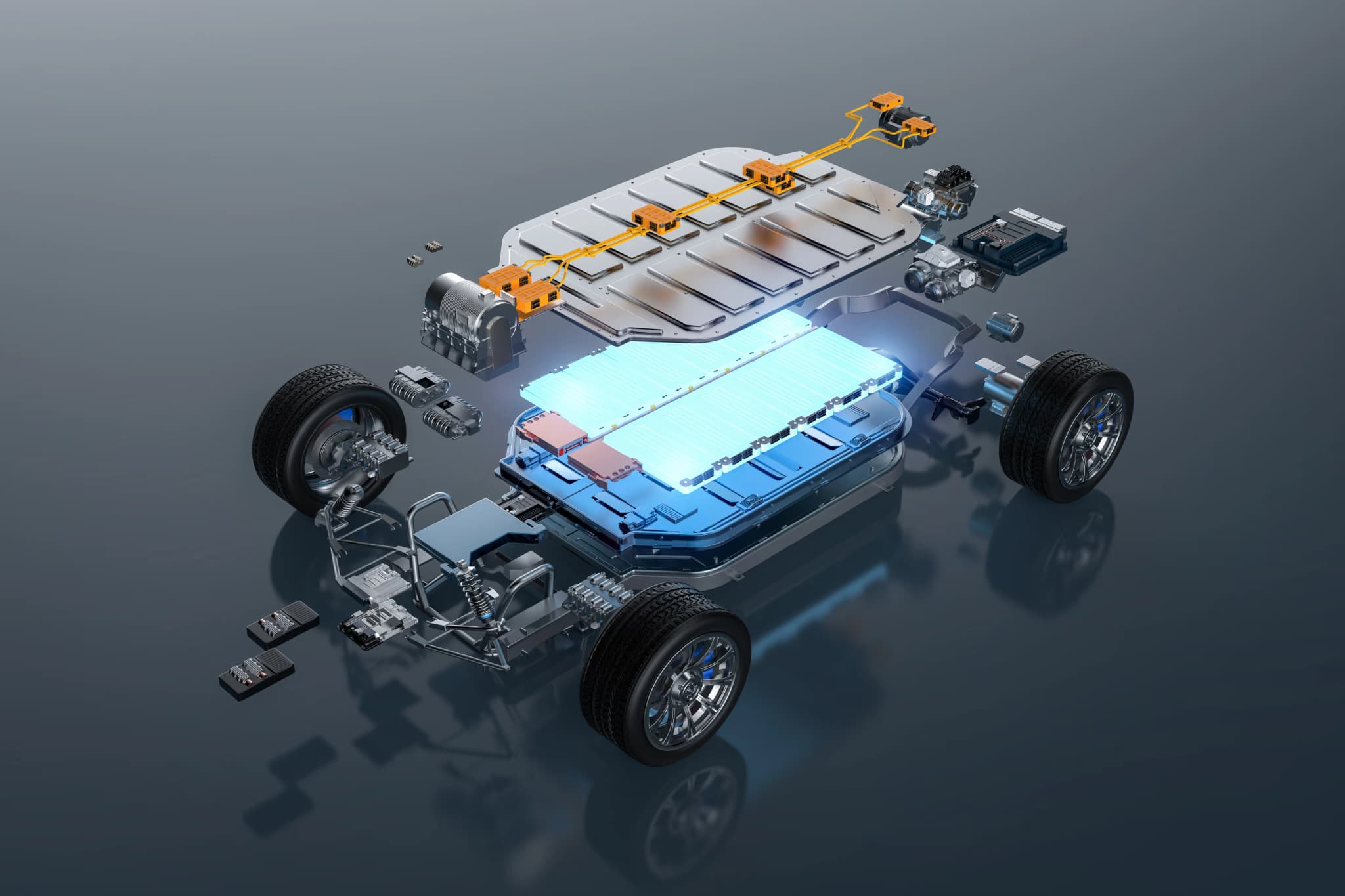
Electric Mobility
Trusted by over 200 FSAE teams worldwide, our lightweight and efficient battery modules power electric vehicles from concept to competition. Achieve top performance with our customizable, plug-and-play solutions.
Learn More About
Our Products
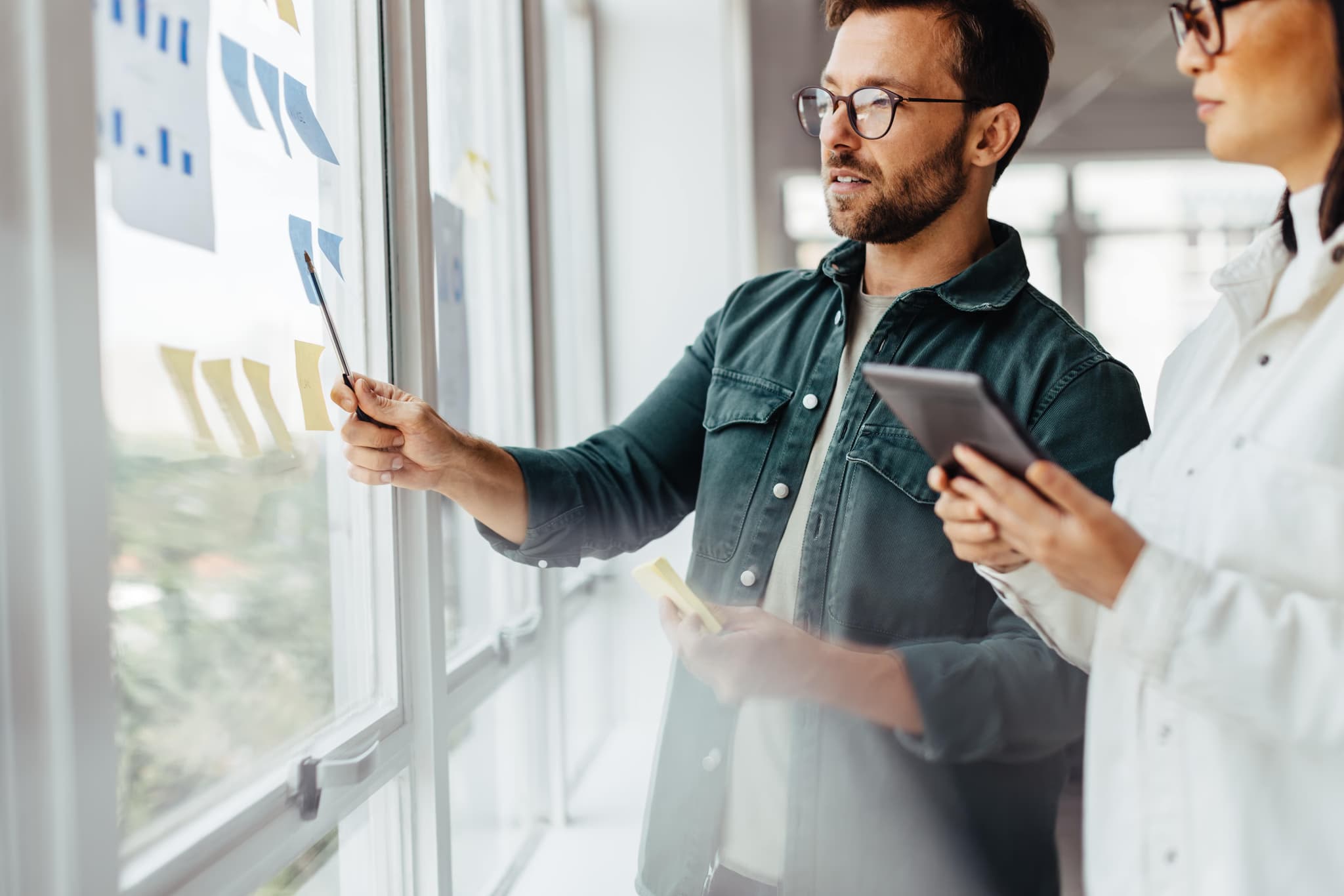
Let’s Build Your Perfect Battery Solution
Unsure which system suits your project? Our experts are ready to guide you in finding for best solution.
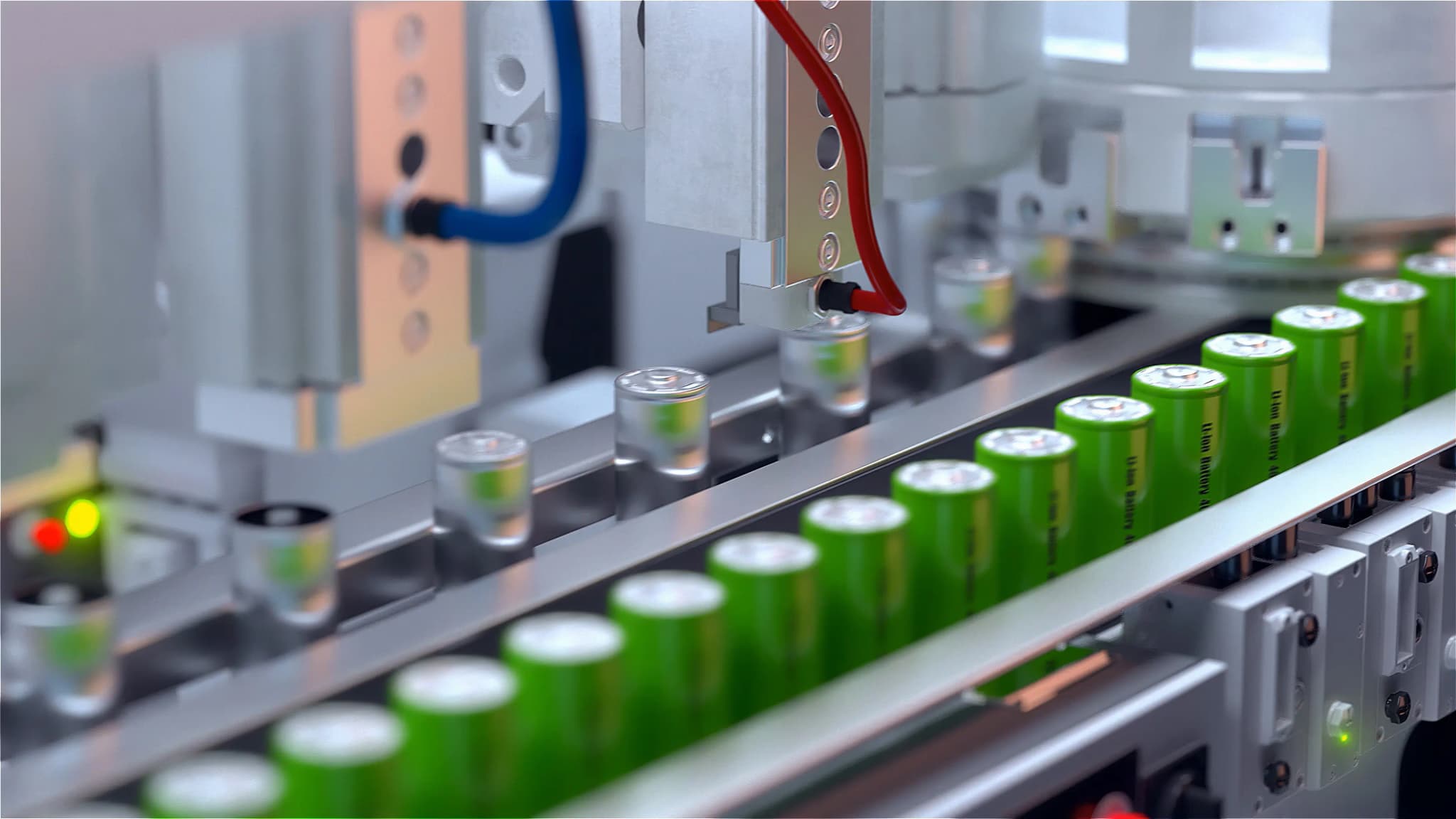
Explore Our Range of Innovative Products
Discover customizable and advanced products designed for every engineering challenge.